With a lot of in-house work and ORBIS: SCHUNK switches to SAP S/4HANA on schedule and under budget
Sectors: Manufacturing industry
Processes: IT
References: Schunk
SCHUNK GmbH & Co. KG is setting the course for further growth with a comprehensive digitalization strategy. A decisive step on this path and towards an intelligent company is the successful system conversion to SAP S/4HANA, supported by long-standing IT partner ORBIS.
In order for industrial robots to precisely grip and securely hold the workpieces, parts or components they process, various end-of-arm components and grippers are mounted on the robot. Leading companies in many industries, such as mechanical and plant engineering, frequently use systems from SCHUNK GmbH & Co. KG.
Headquarter: Lauffen am Neckar
Gripping systems division: SCHUNK grippers, robot accessories, components and services for automated handling
Clamping technology division: Clamping technology for tools and workpieces in metal-cutting processing
Mechanical engineering: depanelling
Locations: nine production sites, 34 subsidiaries and sales partners in over 50 countries
Employees: approx. 3,500 employees (2021)
Group turnover: around 450 million euros (2020)
Website: schunk.com
Market leader in gripping systems and clamping technology
The globally active family-owned company is the competence and world market leader for gripping systems and clamping technology. With 11,000 standard components, SCHUNK offers the world‘s largest range from a single source on the market and, with 2,550 grippers, the widest range of standard gripping components. The complete gripping system programme comprises over 4,000 components.
SCHUNK has always owed its market-leading position to the development and manufacture of innovative, competitively differentiated products and excellent services. The company is setting the course for its future sustainable and profitable growth with a comprehensive digitalisation strategy.
With SAP S/4HANA in the direction of „Intelligent Enterprise“
Digital, standardized and efficient business processes across all locations and business units are also an important part of this strategy. With the SAP Business Suite powered by SAP HANA in conjunction with ORBIS solutions for Manufacturing Execution and Logistics as well as SAP Customer Experience and CRM applications, the foundation has already been laid.
SCHUNK has now taken another decisive step on the way to digitalization, automation and optimization of its processes, i.e. in the direction of an intelligent enterprise, with the system conversion to SAP S/4HANA. As with the introduction of the SAP Business Suite, the company also relied on the consulting, process and technology expertise of ORBIS SE.
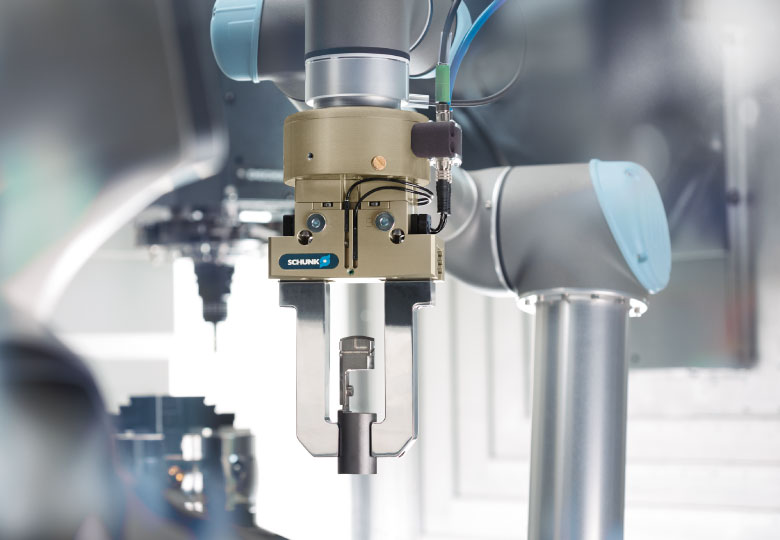
Strong arguments for early changeover
There are important reasons why the conversion to the latest ERP suite from SAP was tackled at this time: Since SAP Business Suite has not yet been introduced in sales offices in particular, SAP S/4HANA can be rolled out there without a diversion, which saves costs. As of today, the mainstream maintenance for SAP Business Suite will also expire at the end of 2027. With SAP S/4HANA, the group of companies can therefore establish a future-oriented SAP system landscape at an early stage and now realise its innovation projects with the latest SAP technologies, which ensures investment security.
Source Photo: © SCHUNK GmbH & Co. KG
On time and under budget with Lean Conversion
Initially, the focus was not on innovation projects, but on rapid and secure conversion, including a custom code check, modification comparison and a check of the code adjustments made for in-house developments and add-ons against the SAP Simplification List. This “lean conversion“ as well as the cooperative partnership between the departments, the internal IT and the ORBIS consultants contributed significantly to the fact that the schedule of the system conversion could be kept and the agreed budget even undercut. The latter is largely due to the coaching approach of the Saarbrücken-based IT service provider, which transfers knowledge very early in the project and thus enables the internal IT to carry out many tasks independently.
Source Photo: © SCHUNK GmbH & Co. KG
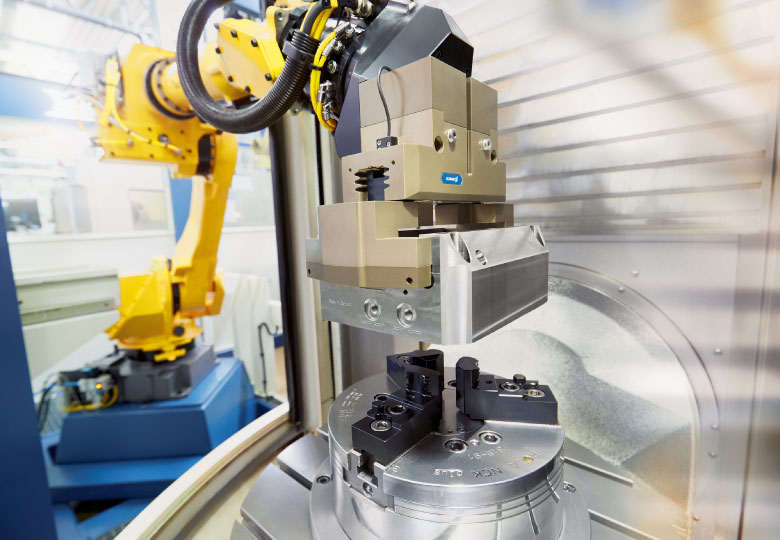
One of the challenges was to merge the data of the customers and suppliers in the central SAP Business Partner. The special requirements of SCHUNK with regard to the contact persons at the customers had to be mapped exactly in SAP S/4HANA. Accordingly, the standard logic of Customer Vendor Integration (CVI) had to be adapted when synchronizing the customer and supplier masters. Parallel to the system conversion, an add-on for foreign trade processes and preference calculation based on the “old“ SAP ECC data model was replaced by a third-party solution, as SAP S/4HANA does not support preference processing and the introduction of SAP GTS was out of the question.
Go-live in one go almost without downtime
The successful implementation of the new ERP suite in five SCHUNK companies in Germany, France and the USA then took place in a big bang. Thanks to detailed cut-over planning, extensive functional tests in several sandboxes, a final acceptance test and additional checks, the downtime until the release of the SAP S/4HANA productive system was kept to a minimum. The downtime until the release of the SAP S/4HANA productive system was kept within narrow limits at just over two days.
But that was just the beginning. SCHUNK is also planning to roll out the new ERP suite from SAP to all other sales offices worldwide. The satisfaction of the end users is to be increased through clear Fiori apps tailored to their needs and the more intensive use of SAP Fiori interfaces. The possibilities offered by the SAP Business Technology Platform (SAP BTP) to make business processes in the individual areas even better and more efficient through the development of innovative and intelligent cloud solutions that extend the ERP core are also being examined.
„Within the framework of our digitalization strategy, we have carried out the changeover to SAP S/4HANA quickly, securely and under budget thanks to active support and advice from ORBIS and the lean conversion approach. The new ERP suite is an important building block on the way to becoming an intelligent company.“
Marcel Schieferdecker
Business information specialist (FH) and IT director IT at SCHUNK GmbH & Co. KG