SUSPA rolls out SAP: A seamless link between China and Germany
Sectors: Steel / Steel Service Center / Metal industry, Mechanical and plant engineering
Processes: Rollout
References: Suspa
Company-wide consolidation of the IT environment and standardization and harmonization of business procedures.
- Intercompany procedures are now automated, swifter and more efficient
- lower process costs within the supply chain
- more efficient warehousing simpler and swifter consolidation of finance
SAP Rollout in China
The implementation of SAP ERP in Chinese production and sales subsidiaries can be continually interchanged by SUSPA with this IT-driven business data. In-house processing among group companies is now swifter and more secure. The subsidiary in China also benefits from the transparent and traceable operating procedures. All this enhances the information available to customers and allows growth to be more efficiently managed.
When there are tasks involving cushioned opening, closing or adjustment, the gas springs, dampers and adjustment systems of SUSPA GmbH often perform such work “noiselessly” in the background.
70 million parts per year
The multinational and innovative SME also develops and produces crash management and security systems and technically complex gears. Each year, SUSPA supplies the vehicle, machine-building and furniture, medical technology and appliance industries with around 70 million parts for 50 products and in 1,500 versions as a system partner
Head office: Altdorf, Germany
Branches: Gas springs, hydraulic dampers
Staff: 1,600 employees, 164 m € turnover
Sites: worldwide
Website: www.suspa.com
The company produces its products in Germany at the head office in Altdorf of Nuremberg and in the Upper Palatinate Sulzbach-Rosenberg location as well as international sites in the Czech Republic, USA, India and China. A global sales network ensures the required proximity to customers in all key markets and excellent service features.
Bringing all subsidiaries together on a single IT platform
„Due to the global presence of our company, end-to-end processes on the basis of modern IT becomes an increasingly important competitive factor“, confirms Jürgen Nothof, Global IT head at SUSPA GmbH.
The scope of the IT strategy thus also extends to consolidating the IT environment on a company-wide basis and standardizing and harmonizing business processes from sales, purchasing, production and storage up to reporting systems.
For this purpose, the gas spring and damper manufacturer wishes to unite all global factories via application engineering at its Altdorf base and establish the SAP procedures defined in the head office as the applicable standards at all its subsidiaries – to the extent legally possible. The basic prerequisites are already in place. For years already, the company has been reliant on structuring its operating procedures based on tried and tested SAP ERP functions. Under the umbrella ERP solution, the factories in Sulzbach- Rosenberg and Bor in the Czech Republic have already been integrated. The customs clearance and external trade, in turn, will be implemented in a manner that is verifiably compliant with the SAP Business Objects Global Trade Services (GTS) application.
SAP instead of Excel in China
As the first non-European company to do so, the Chinese subsidiary in Nanjing has also commenced working with the SAP system. „The SAP rollout in China had become crucial. The Excel solution which had been used up to that point was no longer capable of handling the continual economic growth of the company and the related rise in process requirements“, explains Jürgen Nothof. SUSPA (Nanjing) Co., Ltd., founded in 2001, has a market share of 80 percent in China for washing machine dampers and also leads the way in the provision of gas springs for local vehicle and furniture industries. This subsidiary currently employs 300 people.
SAP rollout in just six months
Nanjing has seen SAP functions installed for materials management, production, sales and shipping as well as financial accounting and controlling. SUSPA entrusted the task of introducing these changes to ORBIS Consulting Shanghai, a branch of the multinational business consulting group ORBIS AG of Saarbrucken.
The entire implementation process, including the process adaptations and the establishment of master data was achieved by the project partners in only six months or so. The combination of a German-speaking project manager and the Chinese-speaking.
Intercompany processes automated
Not long after going live, the benefits of the integrated business processes were already felt. In particular, intercompany procedures, which had previously been performed manually and on paper, were now automated and hence noticeable swifter and more efficient, which helped reduce process costs within the supply chain.
To ensure unhindered communication between the Chinese and the other languages present in the system, SAP ERP also transferred to the Unicode character set prior to the rollout project.
Source Photo: © SUSPA GmbH
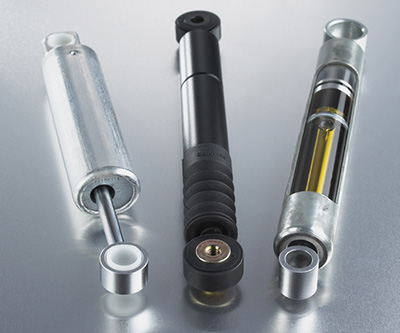
More efficient warehousing
End users in China now have a clear view of the stocks and requirements in storage and can order the required materials – which means more efficient warehousing. Moreover, all inventory record keeping is now traceable, since SAP documents all warehouse movements without fail.
The availability of information for local customers has also been considerably improved. Just a glance at the ERP application is enough for sales employees in Nanjing to determine today, immediately and reliably, whether their order is in production, at the distribution center or already on the way.
„The introduction of SAP in China marks a further step forward on the way to consolidating our IT environment and unifying our cross-factory business processes.“
Jürgen Nothof, Head of Global IT, SUSPA GmbH
Golden tax compliant book keeping
And last but not least, the incorporation of the golden tax system into the SAP software means invoicing is now legally compliant at all times. The use of government fiscal software is compulsory in China, to be able to sell goods to Chinese business partners and obtain refunds on value added tax paid. The Chinese tax authorities also require standardized reports on accounting and payment transactions, claims and debts and balance sheets.
Just a few clicks of the mouse are now all it takes to obtain the required financial and accounting data from SAP ERP, issue the formatted reports and link up with the central tax system, via a bidirectional interface, namely the ORBIS Golden Tax Interface (GTI), to submit files in text or Excel format. Conversely, GTI also converts the files created within the Golden tax system into Excel or text format files which SAP can read and transfers the same into the ERP solution. Since the Chinese subsidiaries now process financial figures and key indicators exclusively in SAP ERP, the process of controlling the same the main office to compile financial statements for the SUSPA group has been consolidated and made far simpler and swifter.
Further developing the IT environment
And there is more Efforts are currently being made to further expand the SAP functionalities in China by cooperating with ORBIS to implement batch management and Warehouse Management (WM).