Oerlikon: Digital and transparent processes in manufacturing with ORBIS MES
Sectors: Steel / Steel Service Center / Metal industry, Electro and electronic industry, Mechanical and plant engineering
Processes: Manufacturing
References: Oerlikon
Implementing the ORBIS Manufacturing Execution System (ORBIS MES) is enabling Oerlikon Balzers to digitalize, optimize and accelerate processes on the shop floor and benefit from transparency in areas such as production control and maintenance. The system’s modern and user-friendly masks, which offer flexible adaptability, have led to a high level of acceptance for the MES among end users. ORBIS SE has been tasked with implementing and rolling out the MES at the company's coating centers worldwide.
Solutions: High-tech surface solutions and polymer processing technologies including services for the automotive, tooling and aerospace industries, the energy sector, and the field of additive manufacturing (3D printing)
Employees: over 12,600
Headquarter: Pfäffikon, Switzerland
Website: www.oerlikon.com
Oerlikon Balzers is a world-leading technology brand specializing in high-tech surface coatings designed to reduce friction and wear on precision components and tools used in metal and polymer processing, thereby significantly improving their performance and service life. More than 1,300 coating systems are used worldwide by Oerlikon Balzers and its customers. Oerlikon Balzers has a dynamically growing network of over 110 coating centers in 35 countries across Europe, North and South America, and Asia.
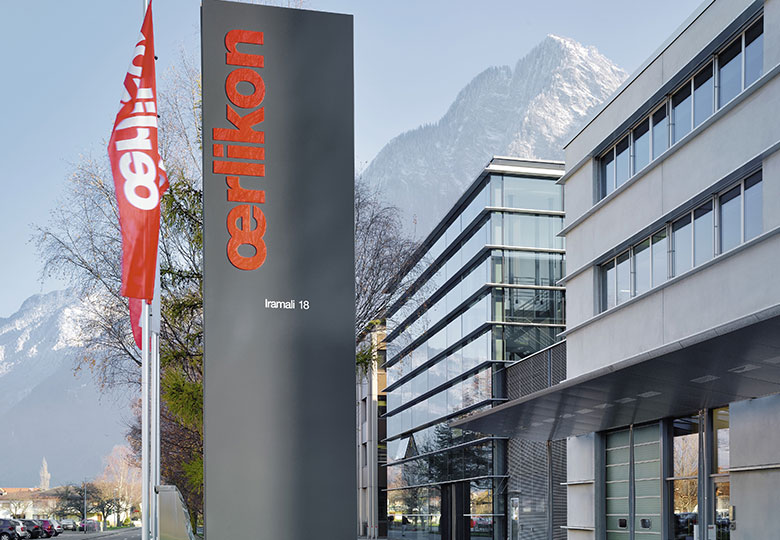
A clear strategy for future growth
Oerlikon Balzers, along with Oerlikon Metco and Oerlikon AM, is part of the Surface Solutions Division of OC Oerlikon Corporation AG (Oerlikon) based in Pfäffikon, Switzerland. The technology and engineering group, which has a workforce of around 12,600 employees at 207 locations in 38 countries and generated sales of 2.7 billion Swiss francs in 2023, operates its business in two divisions: Surface Solutions and Polymer Processing Solutions.
Source Photo: © Oerlikon
Oerlikon is pursuing a clear growth strategy to further expand its leading market position. The focus is on tapping into promising emerging markets and on targeted mergers and acquisitions. Other key factors for economic success include a strong innovative capacity as well as a future-proof integrated IT landscape with digital, transparent, and standardized processes right down to the shop floor.
Shop floor transparency through digital processes
With the global rollout of the business software SAP ERP (SAP ECC 6.0), which replaces a country-specific customised Microsoft ERP, and the SAP-based ORBIS Manufacturing Execution System (ORBIS MES), which integrates seamlessly with SAP ERP solutions, the foundations have been laid.
“The installation of ORBIS MES, which is happening at the same time as the SAP ERP rollout, is a key strategic move to establish standardized digital processes on the shop floor across all plants,” says Dr. Tobias Hanke, Manager Global Strategic Projects GSO / Global PMO at Oerlikon.
Oerlikon is already seeing a variety of positive results through introducing the MES, which is currently being used extensively at 66 coating centers for maintenance and quality management processes as well as for production control. “Shop floor tasks are now completely IT-supported and carried out consistently across all plants. This creates unprecedented transparency in relation to production order progress in Production. It's real added value,” emphasizes Dr. Tobias Hanke. Data quality has also increased, which in turn impacts positively on the accuracy and informative value of shop floor reporting.
Flexible user masks, more efficiency on the shop floor
ORBIS MES also offers the option of combining similar production orders into a single order, bundling them together and sending them through production before reporting them back to the SAP ERP. User workload is significantly reduced as a result. This, combined with the MES’ modern, easy-to-use, and flexible user masks, which have been adapted to Oerlikon Balzers' requirements and allow users to complete their tasks much faster than with comparable SAP functions, constitute two further advantages. Thanks to all this, there is a high level of acceptance for the MES among the more than 2,374 active end users worldwide, who enjoy working with the system.
“The adaptable user masks have also made it possible to map one of our core processes in ORBIS MES with batch reporting, where production orders for different parts are reported back to the ERP in bundles. We've also been able to set up a completely new digital and efficient mobile process flow for maintenance," explains Dr. Tobias Hanke.
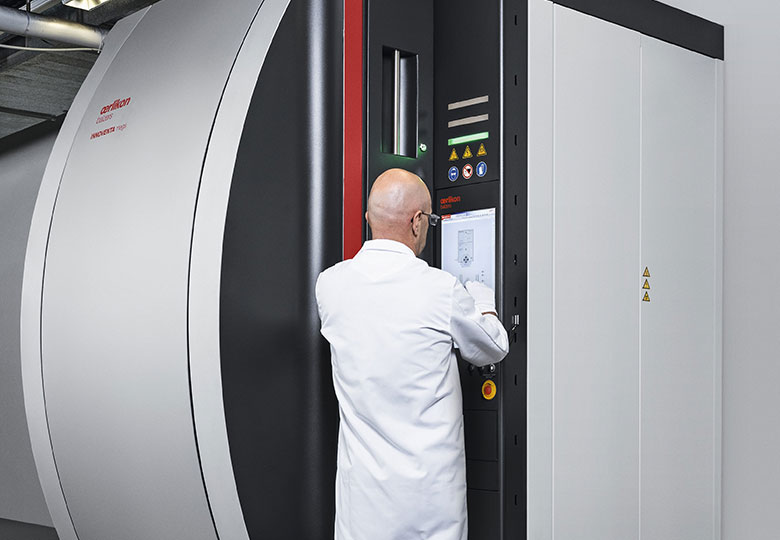
Technicians can now conveniently and quickly complete arising maintenance-related tasks with just a few actions on a tablet (Apple iPad), and directly on site at the specific maintenance point. Such tasks range from accessing the SAP maintenance order or maintenance/fault report, to logging installed spare parts, working hours and external services, to evaluating inspection lots, and capturing and updating measurement point information for maintenance-relevant parts via the MES. This is an important aspect, as the maintenance team uses these measurement values to determine whether a part requires further maintenance. Some of the measuring points are also linked to SAP maintenance plans, which automatically generate a maintenance order as soon as a measured value exceeds the defined threshold.
Source Photo: © Oerlikon
MES introduction and rollout with ORBIS
ORBIS SE was tasked with the challenging implementation and template-supported rollout of the MES in Oerlikon Balzers' various coating centers. The IT service provider made a strong impression with its wide-ranging expertise regarding shop floor processes and their design, as well as its solid international presence.
Thanks to the partnership-based collaboration between the internal project team, key users, and ORBIS experts, plus the high level of commitment of all those involved, the challenging MES implementation was completed quickly and on budget. And this was achieved despite the fact that a global template had to be created for the rollout to more than 110 coating centers worldwide and that process adjustments had to be made to ORBIS MES on an ongoing basis due to the parallel SAP ERP implementation. A considerable amount of work also went into adapting around 30 MES user screens, which had to be designed and optimized according to the individual process requirements at Oerlikon Balzers.
Interoperability with ORBIS DSP
“ORBIS MES is enabling us to bring significantly more transparency and speed to our shop floor processes, noticeably increase productivity and, at the same time, create important prerequisites for digital production in the sense of Industry 4.0,” summarizes Dr. Tobias Hanke.
The next steps are already in the pipeline: rollout of the MES at further coating centers, the introduction of the MES-integrated planning component for scheduling and sequencing production orders, and the connection of production plants. The use of AI technologies is also being considered in relation to optimizing capacity planning for coating, pre-treatment and post-treatment systems.
But that isn’t all. Oerlikon Balzers is set to use the ORBIS Distributed Shopfloor Processing (ORBIS DSP) solution to establish interoperability between technical data and processes at production level, a new IoT platform based on AWS, and business systems such as ORBIS MES and SAP ERP. The proof of concept (PoC) has already been completed. ORBIS DSP is currently being implemented as part of a pilot project at a coating center in Brügg, Switzerland. The EDGE component of the DSP solution is being operated using industrial-grade control cabinet-based hardware. Those responsible for the project see a major advantage in being able to use the ORBIS DSP cloud-based Management Cockpit to centrally configure and manage the large number of coating centers worldwide, the systems installed there, and data and process flows.
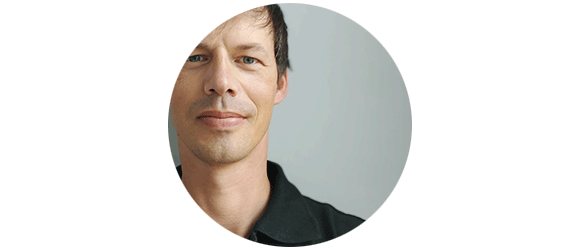
“ORBIS MES is enabling us to bring significantly more transparency and speed to our shop floor processes, noticeably increase productivity and, at the same time, create important prerequisites for digital production in the sense of Industry 4.0.”
Dr. Tobias Hanke, Manager Global Strategic Projects GSO / Global PMO, Oerlikon Surface Solutions